This elegant home is located in Gladwyne, Pennsylvania. Because of an inspection that uncovered water infiltration through stone and stucco, stucco remediation and proper stone-window flashing details had to be addressed and executed. In previous stucco locations, on this home, we installed James Hardie Cedarmill 8-1/4” fiber cement siding with Azek Premade corners, Azek Trim boards and Azek mounting blocks. This siding is from the James Hardie Statement Collection in Khaki Brown, which really bonds the earth tones of the stone and the neighborhood in which this Montgomery County home is located.
In the first stage of this project, scaffolding was set up with a plastic enclosure, on the front, stone wall of the home. Because chipping guns were used to carefully remove stone from around the windows, the landscaping below was protected with plywood, tarps and trash cans. Each stone was meticulously detached from the home and cleaned of loose mortar. Windows were then removed and rough opening framing was inspected before each window rough opening received custom aluminum sill pans and drip caps. Once reinstalled, the exterior perimeter received Tyvek flashing tape and was nailed with hand nails. Each stone had been carefully marked by location to help with the puzzle of piecing it all back together correctly. A mixture of matching mortar was prepared and the surrounding window units were pointed. Because of the cold temperature, a heater was stationed at the bottom of the plastic-enclosed scaffolding to help the mortar properly cure.
In the second stage of this home exterior project, ladders and planks were set up in various stucco locations around the house. Once again, all landscaping was protected using tarps and plywood. Manageable squares were ground into the home’s exterior stucco walls. Once ground, these squares were gently pried off the wall for disposal. The sheathing and the structural integrity was inspected. Areas of deteriorated sheathing were carefully removed, and the insulation and structure were then inspected, before replacing the voids with new ½” CDX plywood sheathing. Benjamin Obdyke HydroGap (Vapor Barrier) was then installed with staples and all seams were taped. Windows within these stucco locations also were removed and the rough opening framing was thoroughly examined. Several rough openings had deterioration and new rough openings were re-framed using framing lumber. Once rough openings were ready for existing window installation, each opening was properly flashed just like the windows within stone. Azek (PVC) details were installed around windows, corners, and transitions before beginning new residential siding installation using James Hardie fiber cement siding in Khaki Brown.
New residential siding was installed at a 7-inch exposure using ring shank coil nails. All butt joints were flashed with aluminum and cut edges were sealed with color match James Hardie touch-up paint, Khaki Brown. All transitions were carefully caulked using OSI Quad sealant, also in James Hardie Khaki Brown. Once all James Hardie siding and PVC details were installed, all PVC (white) was painted to match existing rakes, rascias, and soffits. In water prone locations, custom aluminum kick out water diverter flashings were installed. These locations include, but are not limited to, locations where gutters meet new siding.
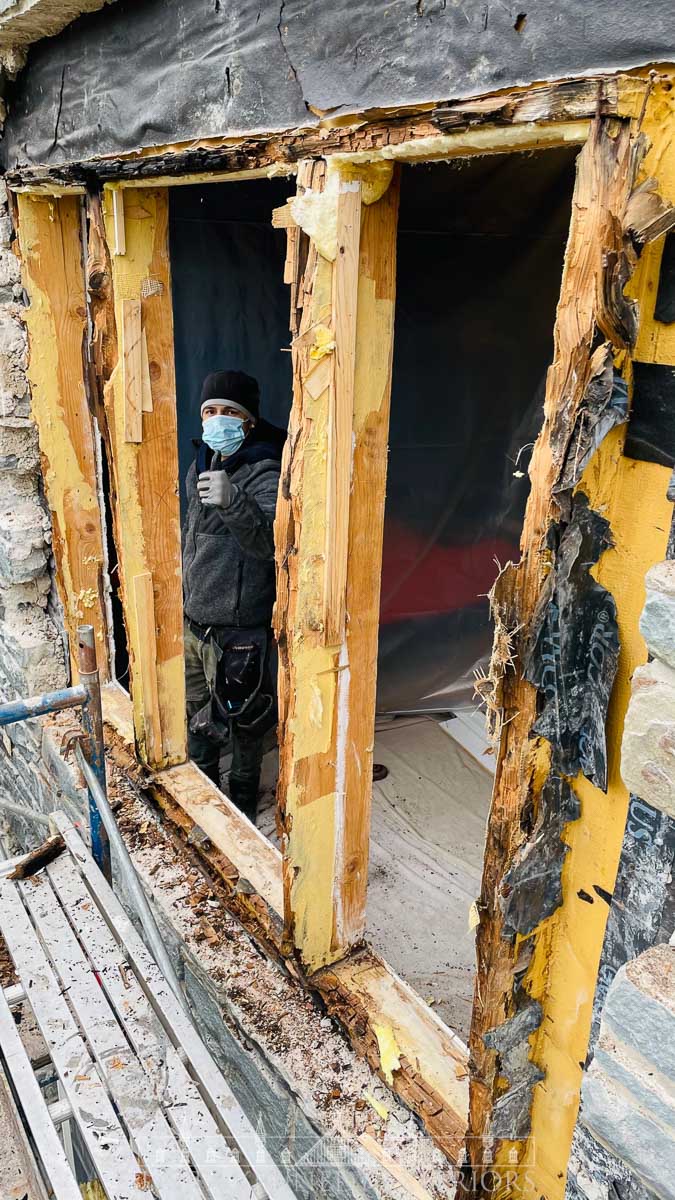
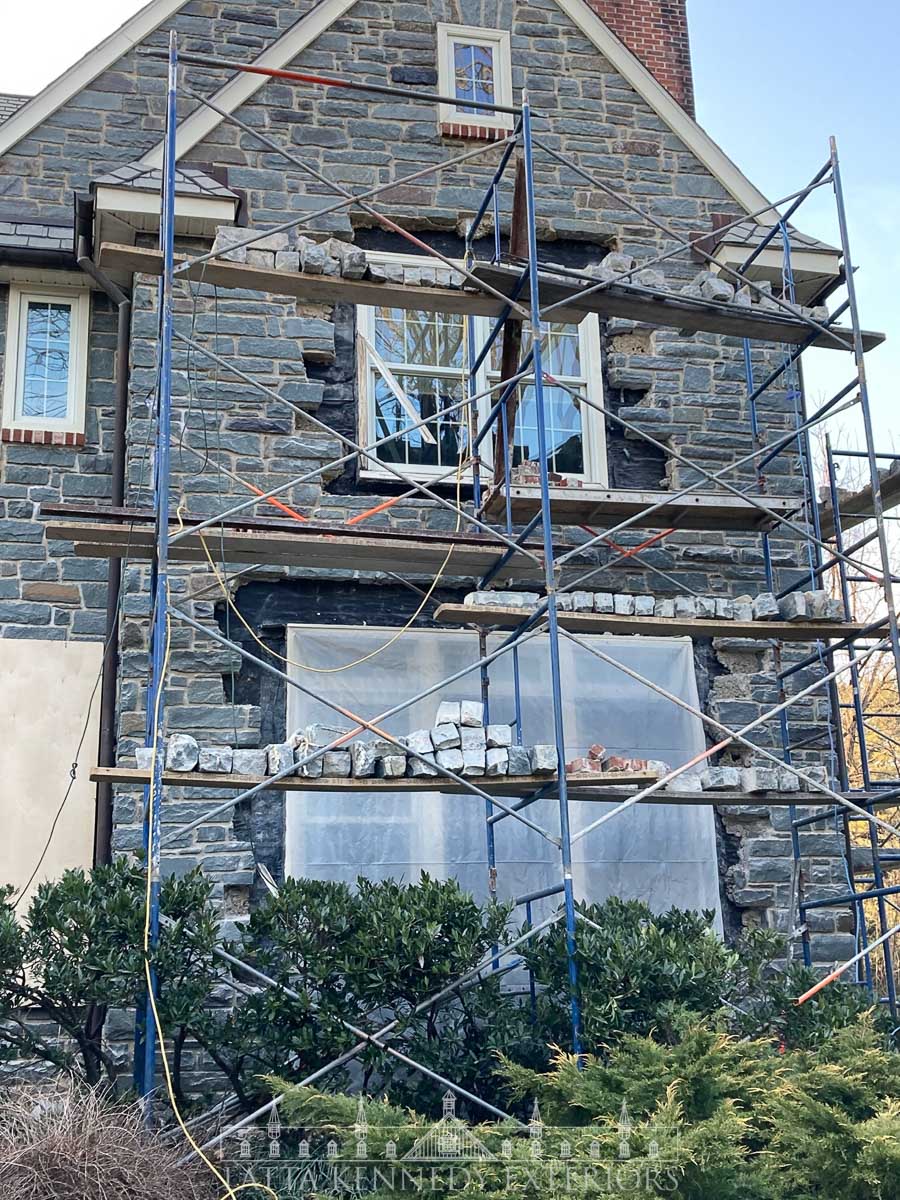
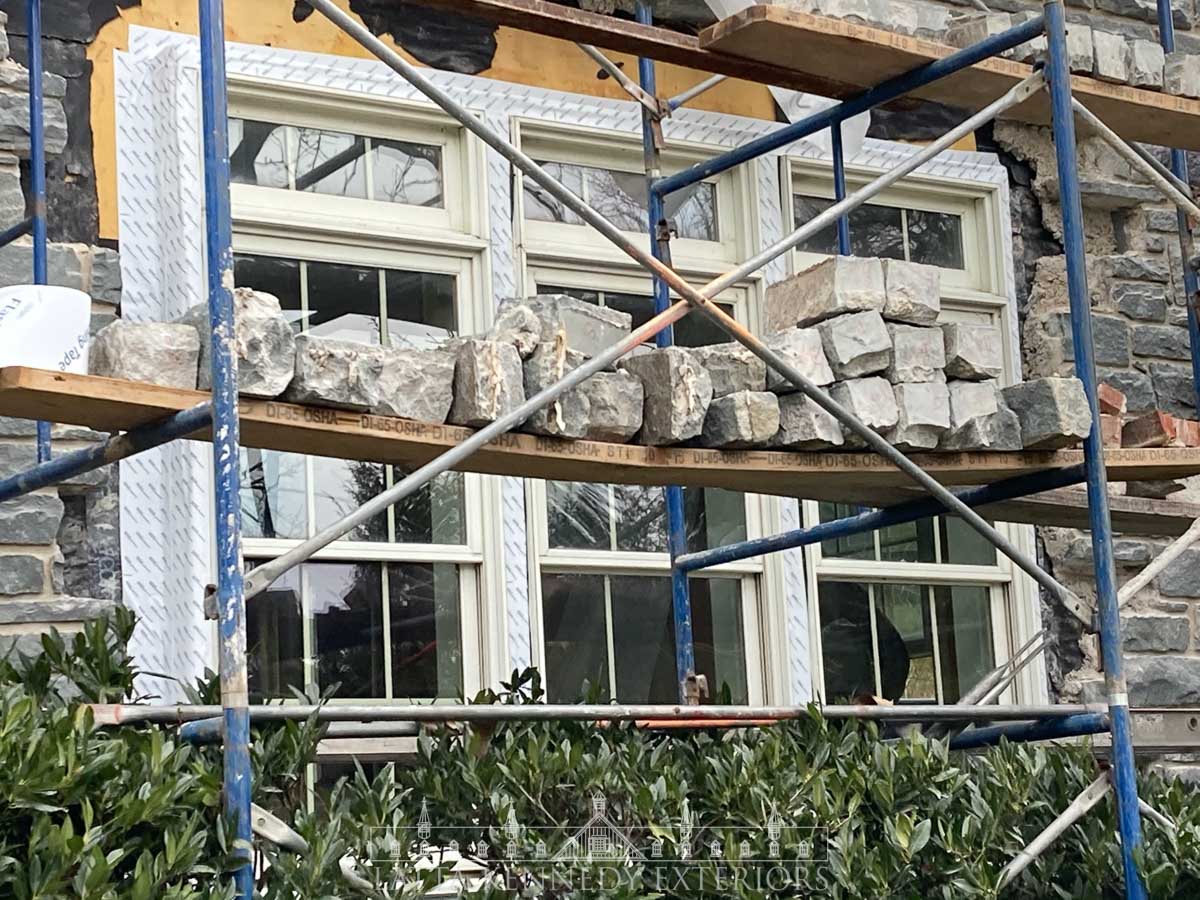
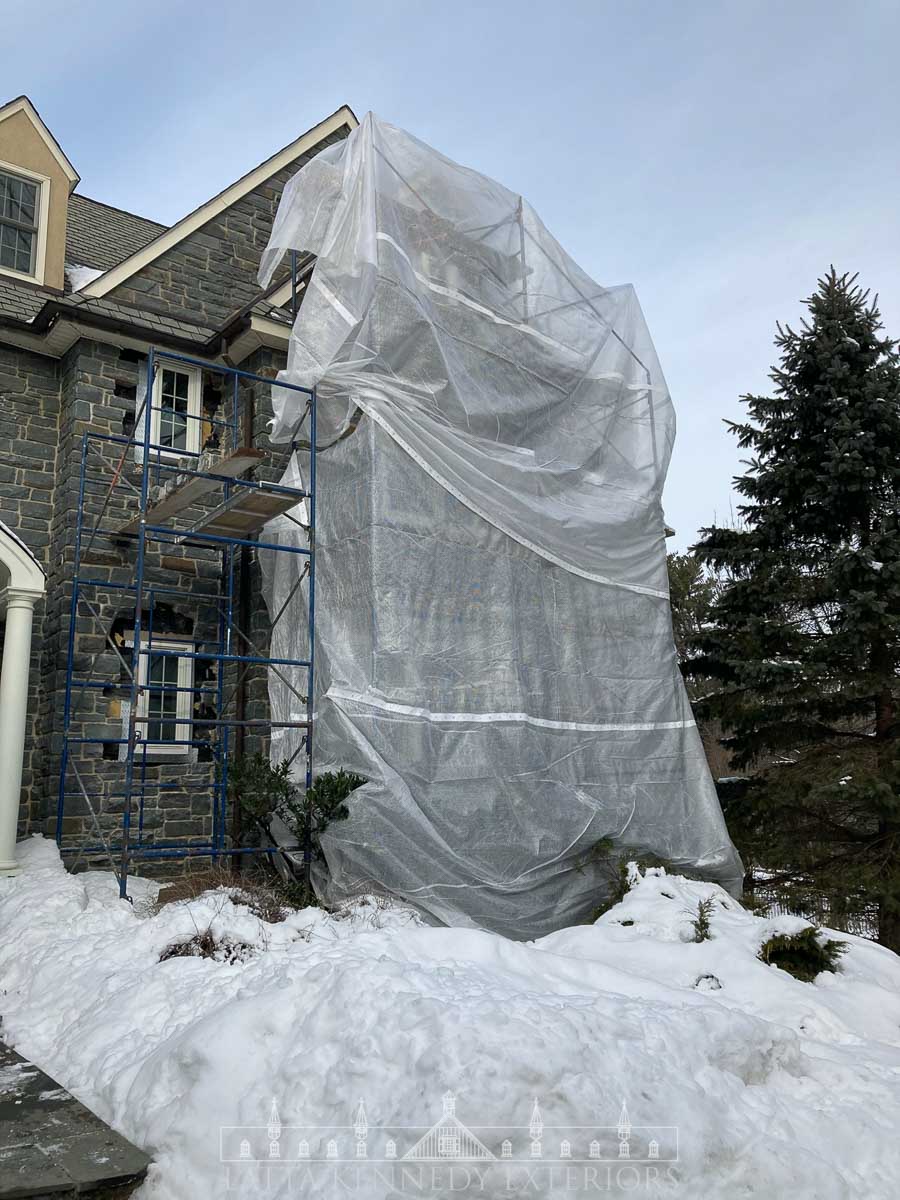
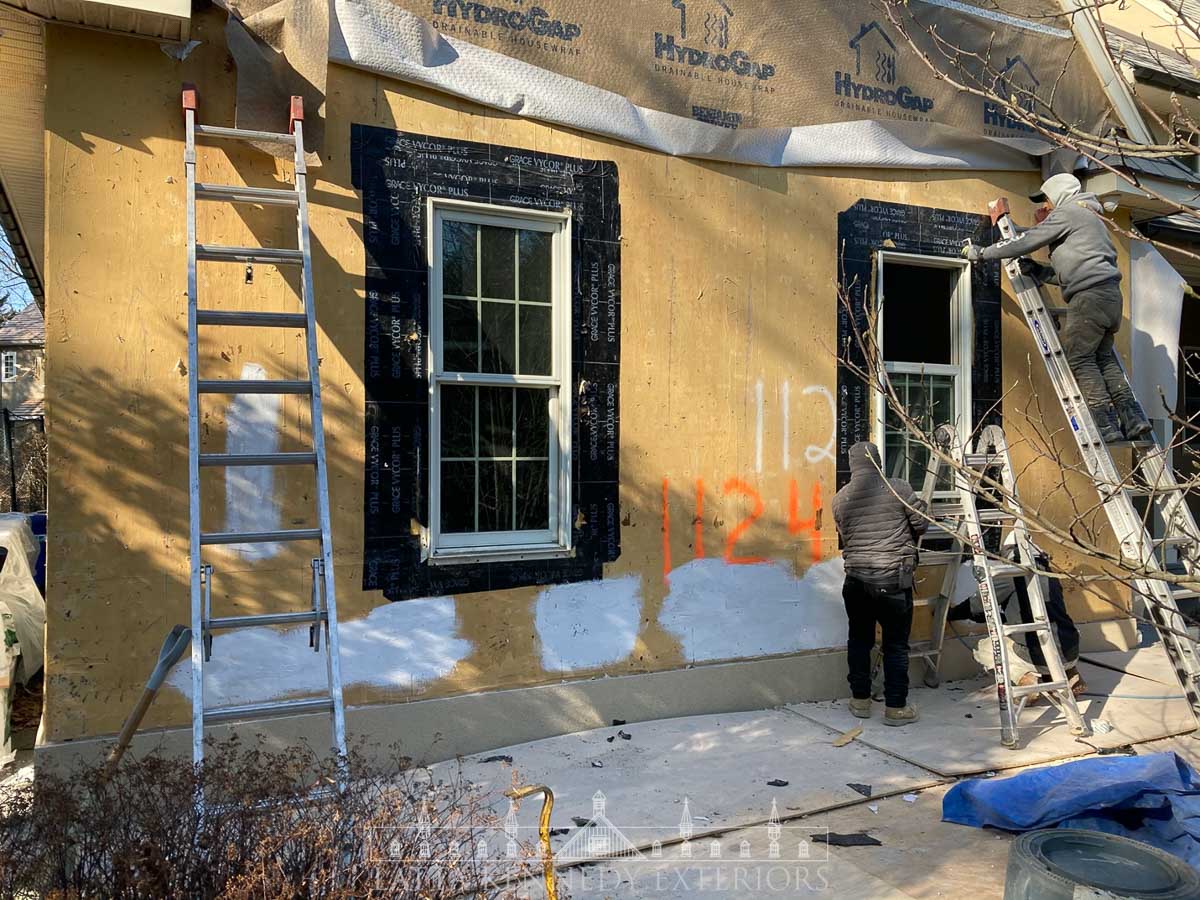
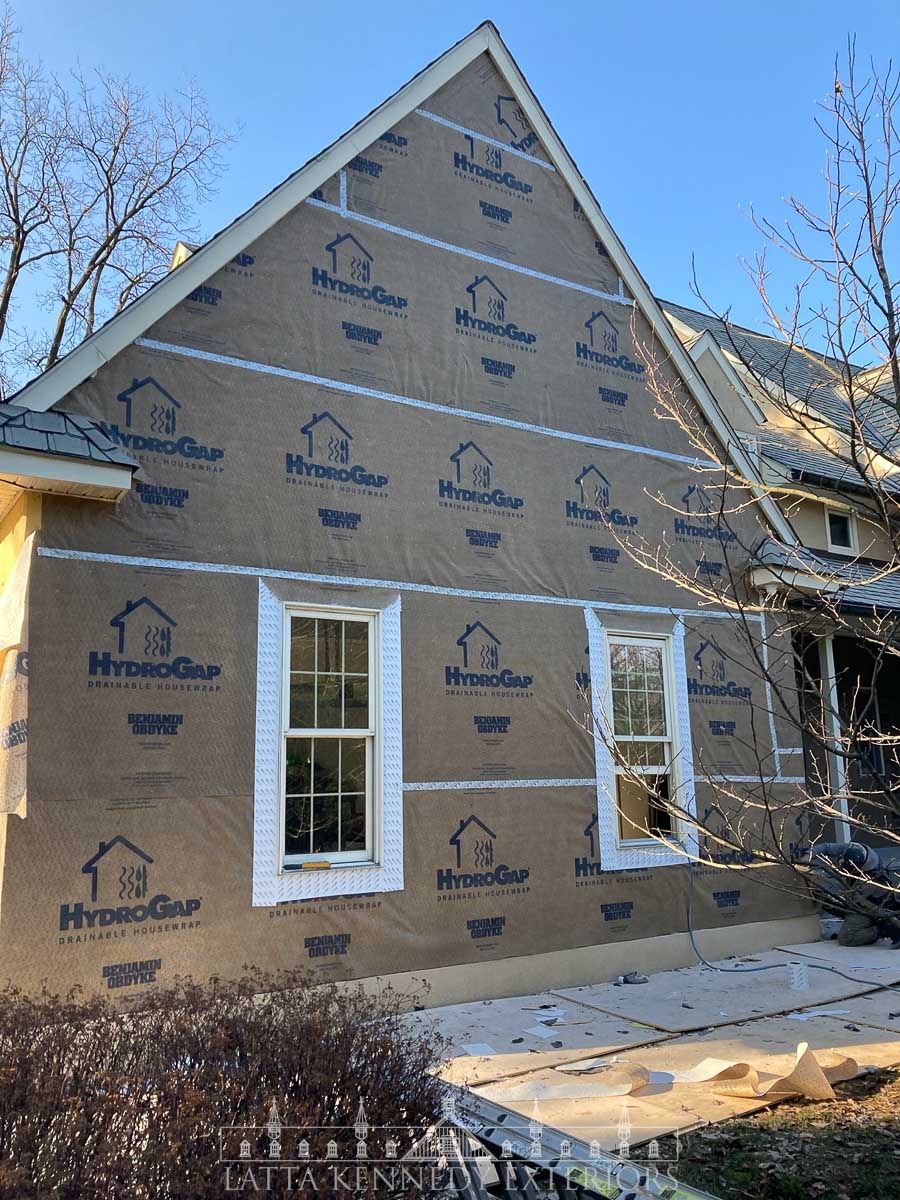
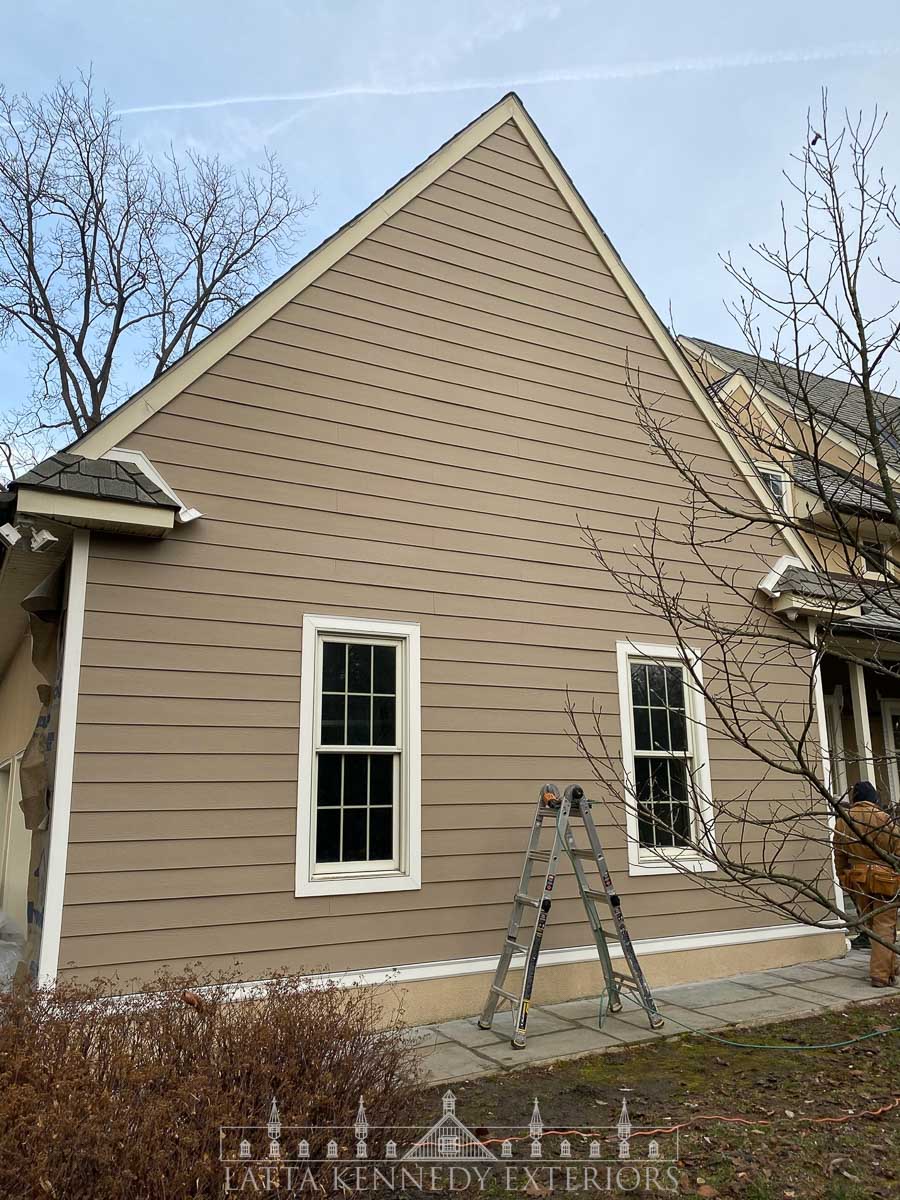
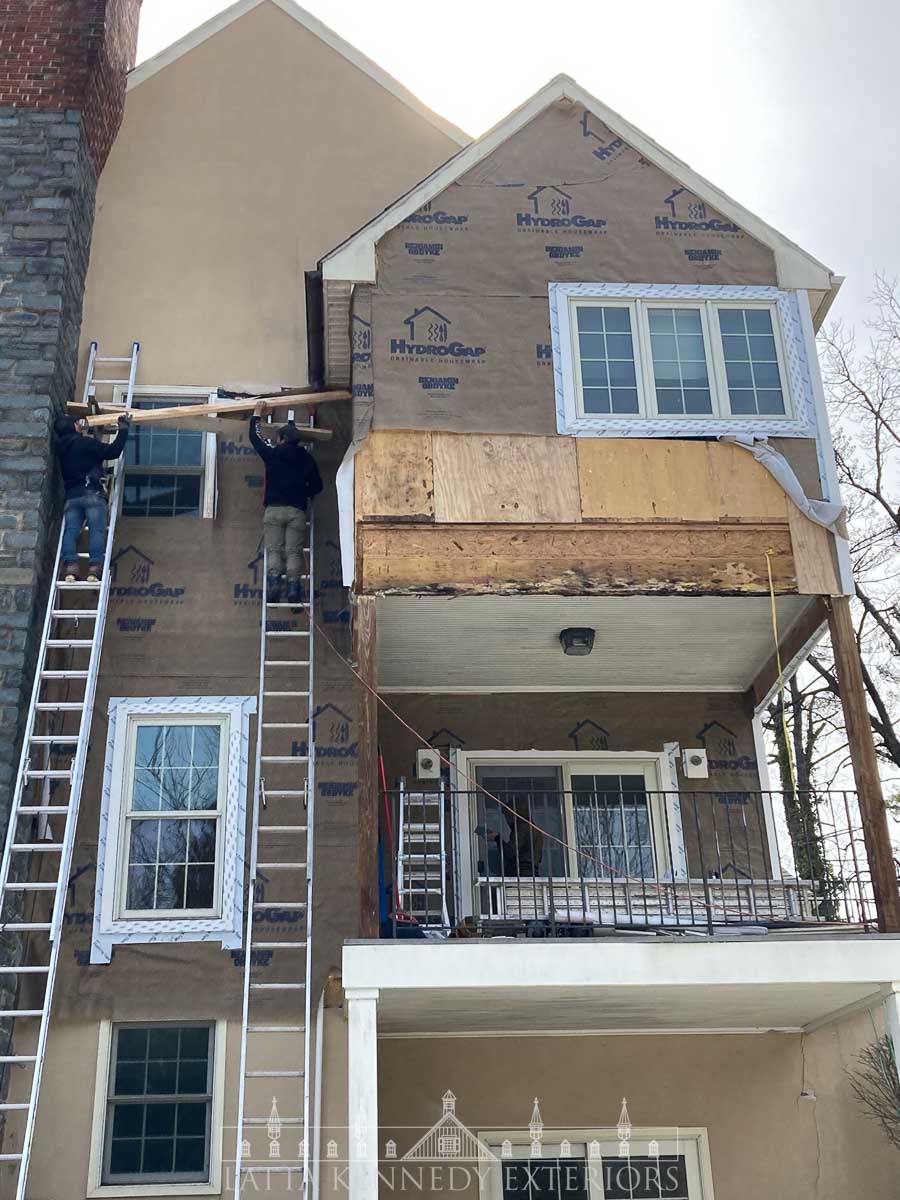
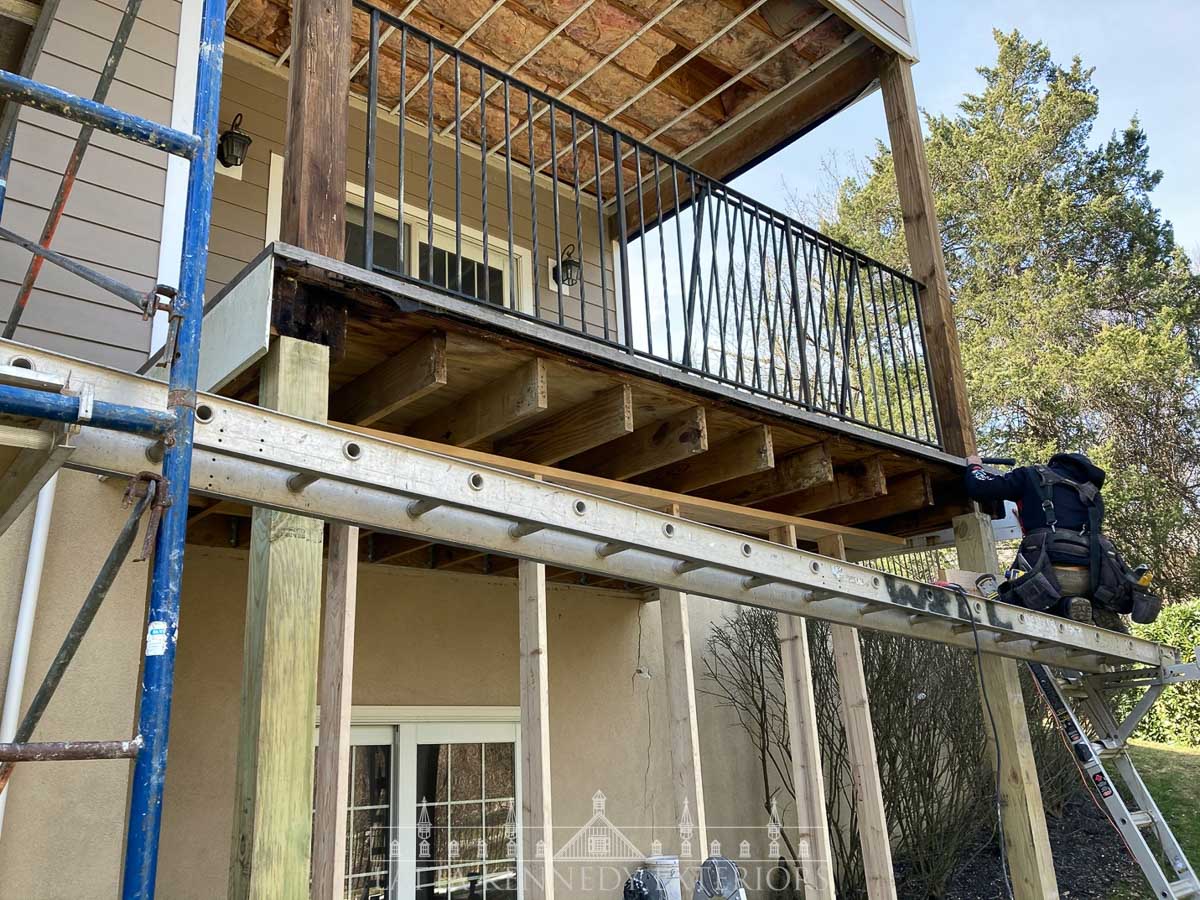

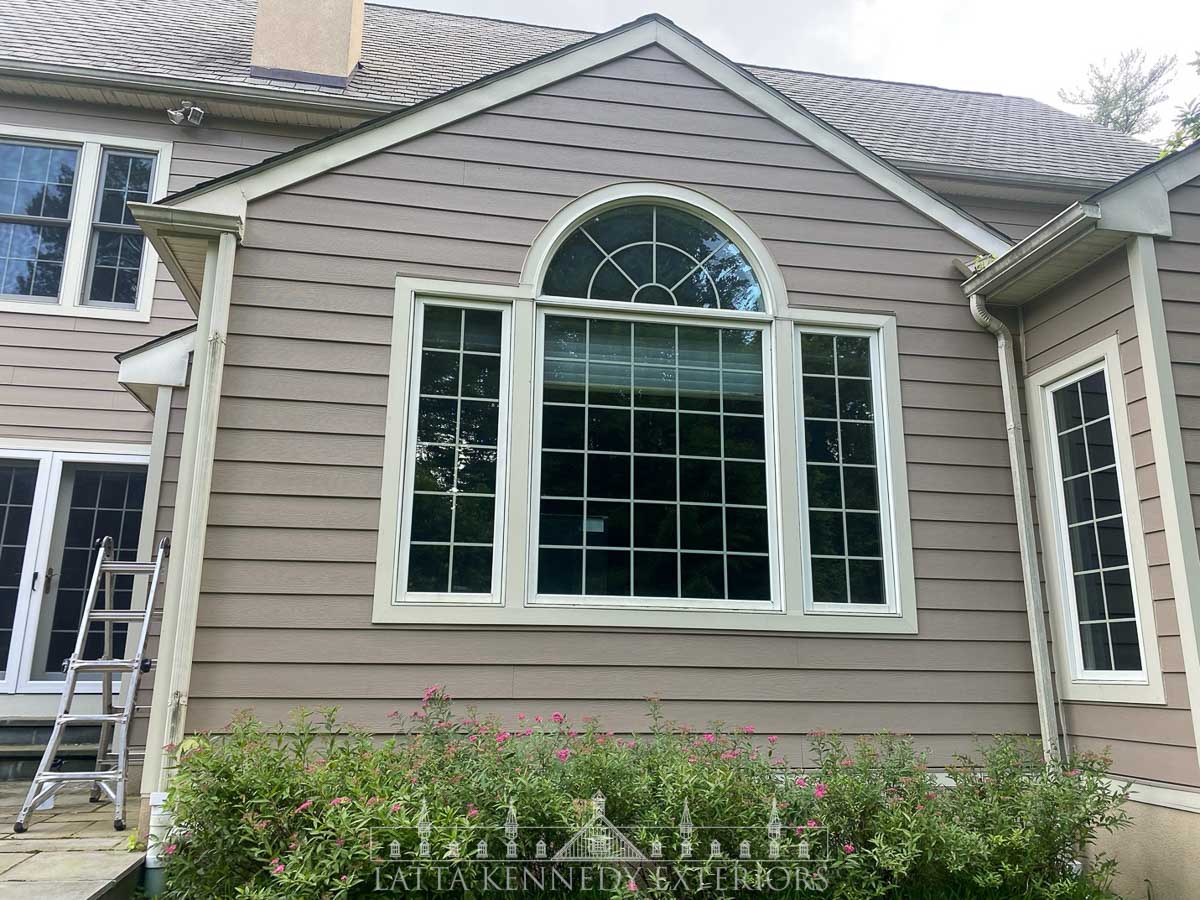